DOL Starter method is a common method of starting of Cage Induction Motor. The motor is connected through a starter across the full supply voltage. The Direct On Line Starter Method figure is shown below. It consists a coil operated contactor C controlled by start and stop push button as shown in the connection diagram below:

The buttons which may be installed in a convenient place away from the starter. The start button is held open by a spring. On pressing the START pushbutton S1, the contactor C is energised from two line conductors L1 and L2.
The three main contacts M and the auxiliary contact A are closed. The terminals a and b are short-circuited. The motor is then connected to the supply mains. The S1 button moves back under the spring action as soon as the pressure is released. The coil C remains energised through ab.
Thus, the main contact M remains closed, and the motor continues to get supplies. Therefore, contact A is known as Hold-On-Contact. The stop button S2 is normally held closed by the spring. If the S2 button is pressed to STOP the motor, the supply through the contactor coil C is disconnected. As the coil C is de-energized, the main contacts M and the auxiliary contact A are opened. The supply to the motor is disconnected, and the motor is stopped.
Under voltage(UV) Protection
When the voltage falls below a certain value or when the supply fails or disrupted during the operation of the motor, the coil C is de-energized. Hence, the motor is disconnected from the supplyOverload Protection
The motor is overloaded, one or all the overload coils (O.L.C) are energised. The normally closed contact D is opened, and the contactor coil C is de-energized to disconnect the supply from the motor. Fuses are provided in the circuit for short circuit protection.
In direct on line starting the starting current may be as large as ten times the full load current, and the starting torque is equal to full load torque. Such a large starting current produces an excessive voltage drop in the line which supplies power to the motor.
Theory of DOL Starting of Induction Motor
Let,
- Ist be the starting current drawn from the supply mains per phase.
- Ifl is the full load current drawn from the supply mains per phase.
- Ʈest is the starting torque.
- Sfl is the slip at full load.
As we know that the rotor copper loss = s x rotor input
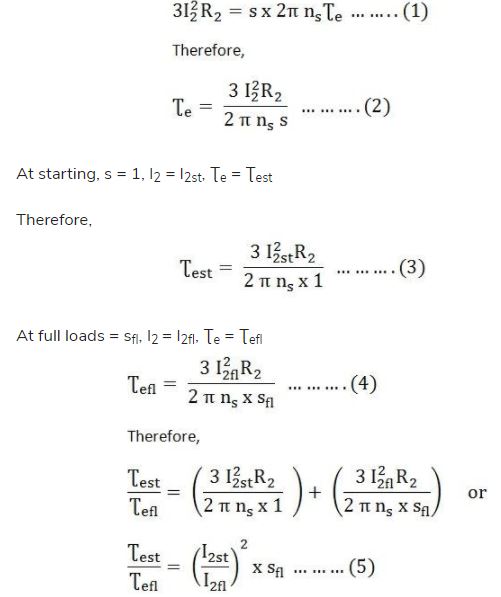

If V1 is the stator voltage per phase equivalent
Ze10 is the standstill impedance per phase of the motor referred to the stator then the current at the starting is given by the equation shown below.
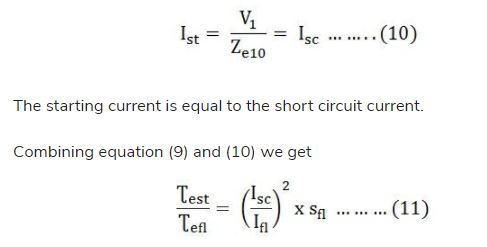
Direct on line starter method is the cheapest and the simplest method of the starting of the induction motor.
Advantages of DOL Starter
The advantages of a DOL starter include:
- Simple and most economical starter.
- More comfortable to design, operate and control.
- Provides nearly full starting torque at starting.
- Easy to understand and troubleshoot.
- DOL starter connects the supply to the delta winding of the motor.
Disadvantages of DOL Starter
The disadvantages of a DOL starter include:
- High starting current (5-8 times of full load current).
- DOL Starter causes a significant dip in voltage, hence suitable only for small motors.
- DOL Starter reduces the lifespan of the machine.
- Mechanically tough.
- Unnecessary high starting torque
Applications
The applications of DOL starters are primarily motors where a high inrush current does not cause excessive voltage drop in the supply circuit (or where this high voltage drop is acceptable).
Direct on line starters are commonly used to start small water pumps, conveyor belts, fans, and compressors. In the case of an asynchronous motor (such as the 3-phase squirrel-cage motor) the motor will draw a high starting current until it has run up to full speed.